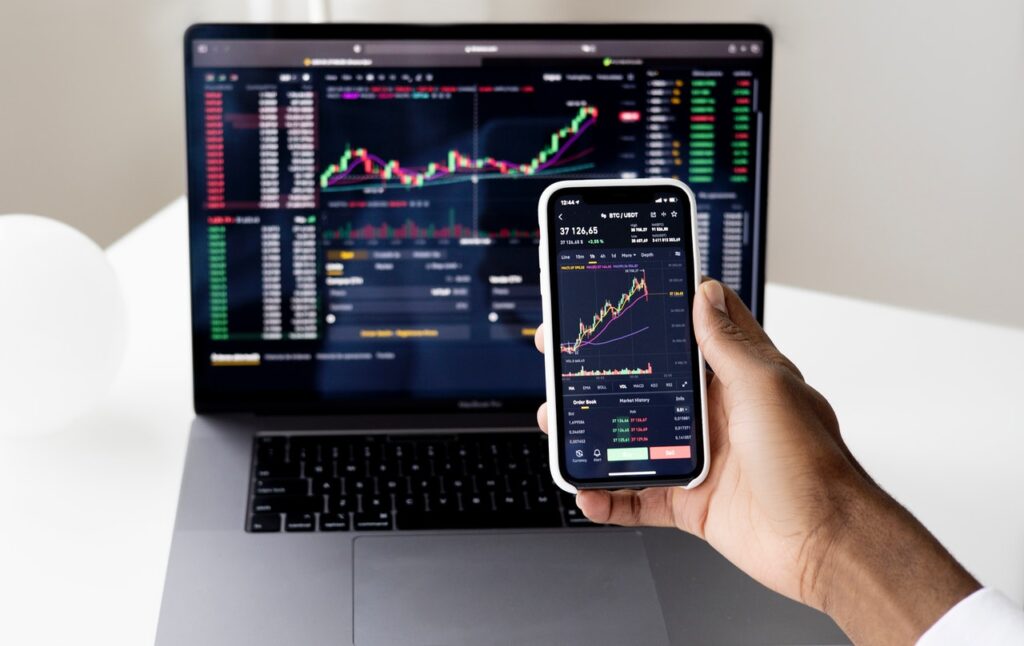
Amble costs have shot up again in an ascent suggestive of a year prior, while high-climbing Lumber prices cautioned of the hinky supply lines and expansive expansion to come.
Fates for January conveyance finished Friday at $1,089.10 per thousand board feet, double the cost for a brief conveyance in mid-November.
Cash costs are far up too. Evaluating administration Random Lengths said that its outlining composite file, which tracks on-the-spot deals, has hopped 65% since October, to $915. A $129 gain this week was the greatest on record, obscuring a $124 bounce in May, when timber costs peaked at record-breaking highs.
However stumble is exchanged elusive business sectors, two-by-fours turned into an intermediary in the discussion about whether expansion would blur with distance from the lockdown. In June, Federal Reserve Chairman Jerome Powell highlighted amble costs plunging from a stunning top as proof that flooding expenses would die down. On Wednesday, he said the national bank would rush the breeze down of its security purchasing program, making way for a progression of loan fee climbs intended to tame expansion.
Amble costs have a best approach before they compromise the records set in spring, when prospects hit $1,711.20. All things considered, stumble costs with a comma were impossible before the lockdown, when factories were surprised by DIY and home-building blasts and every one of the decks expected to work with open air feasting.
Notes on the NewsSIGN UP
Examiners and dealers say conditions are ready at costs to continue to move through winter, as they frequently do in front of the spring building season.
Flooding in British Columbia has removed sawmills from backwoods and clients, abnormally warm harvest time climate has broadened the structure season and wood purchasers are stacking up in anxiety toward additional cost increments and supply issues.
The possibility of higher loan costs cooling the hot real estate market additionally lingers. Higher getting expenses would diminish purchasers’ capacity to stay aware of the cost climbs that developers have used to counterbalance their own expanded expenses. Most Fed authorities have planned for somewhere around three quarter-rate point rate increments one year from now.
“Manufacturers imagine that they’re drawing near to the furthest limit of a cycle and they’re doing all that they can to get houses rolling,” said Matt Layman, an expert and specialist who distributes Layman’s Lumber Guide. “They realize they can pay $1,500 for two-by-fours. They tried to avoid it, however it didn’t hurt them.”
Irregular Lengths said that request has surpassed supply, provoking sawmills to forcefully bring costs up in order to slow requests that are upholding into the new year. “A few makers incapable to prevent purchasers with protective evaluating went off the market,” the exchange distribution said.
What effect has the excessive cost of wood had on your structure or rebuilding endeavors?
Sawmills in British Columbia have marked down yield since downpours cleaned out streets and rail routes last month, sending costs higher for the northwest’s tidy, pine and fir. Occupied developers pounding away through refreshing fall climate ran to eastern business sectors for wood, pushing up costs around the Great Lakes and in the South.
In a new overview of building-item vendors, 20% of respondents let John Burns Real Estate Consulting know that they held what they considered to be overabundance stock of timber, down from 56% who said in August that they had all that could possibly be needed available.
The firm anticipates that home development should speed up in 2022 and solid development in major renovating occupations because of the record measure of home value accessible to pay for new kitchens and increases.
“They should be perched on more stock,” said Todd Tomalak, who tracks building items for the counseling firm. “It’s the powerful coincidence for one more flood of building-item deficiencies, a do this process again in amble and for a ton of other stuff also.”
On Wednesday, the National Association of Home Builders said its list of manufacturer certainty, however down marginally from last pre-winter’s pinnacle extravagance, hit one of its most hopeful readings tracing all the way back to 1985. On Thursday, the Commerce Department said that development began on 1.679 million homes last month at an occasionally changed yearly rate. That is up 12% from October and the most since March.
The quantity of begun homes surpassed those that were finished by the biggest edge beginning around 1984, when twofold digit contract rates failed the real estate market. The enormous hole mirrors the trouble manufacturers have had getting materials, apparatuses and installations important to complete houses.
Manufacturers experience had no difficulty raising costs to balance their own expanded expenses, on the grounds that ultralow contract rates have kept regularly scheduled installments reasonable. Notwithstanding record costs for stumble and different materials, home manufacturers have been revealing a portion of their most noteworthy overall revenues of all time.
Manufacturers including Toll Brothers Inc. , Lennar Corp and Hovnanian Enterprises Inc. let’s assume they are as yet managing the timber purchased when costs topped in spring and anticipate that edges should increment later one year from now when they sell houses worked with wood bought after costs crashed back to earth this late spring. Leaders with those organizations told financial backers during late calls that they are certain they can raise home costs more assuming wood makes one more run.
“The market simply feels truly amazing with respect to evaluating potential open doors, so we’re agreeable,” said Ara Hovnanian, CEO of his eponymous firm, which sold homes at a normal cost of about $445,000 in the monetary year that finished Oct. 31, contrasted and generally $419,000 every year sooner.